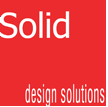
Consumer Product Development
Spotlight
Company: Activar Technical Products Group
Industry: Industrial Centrifuges
HQ: Hopkins, MN
Webpage: https://www.activartpg.com/revolution-centrifuge

The Company was established fifty-four years ago as Reuter Manufacturing, Inc., concentrating on precision machining and assemblies. In early 2001, the Company changed its name to MagStar Technologies, Inc. and then to Activar Technical Products Group a few years later. The Company's contract manufacturing business has been concentrated in the medical device field, which includes production of blood centrifuges, blood analysers, thrombectomy proximal motors, organic chemical synthesizers, and valves for medical oxygen delivery.
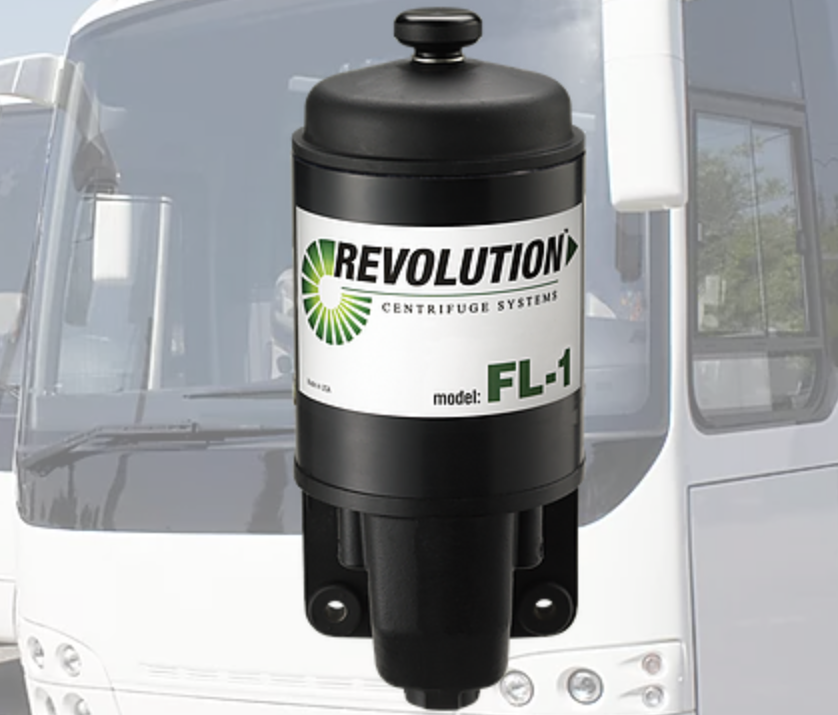
Product/Project Highlights
Oil Filtering Centrifuge
Client: MagStar Technologies, Inc.
- Reduces engine wear
- Significantly extends the useful life of engine oil
- Reduces downtime for oil changes by reducing the number of them required
- Extends engine life

Situation:
Magstar Technologies (now called Activar) approached Solid to provide the engineering design and development needed to create a centrifuge based oil filtration system for long haul semi tractors. Magstar Technologies already had a product line of blood centrifuges for medical laboratory applications and wanted to branch into a secondary market.
Oil Filtering Centrifuge
Client: MagStar Technologies, Inc.
Process:
Solid participated from the beginning through production following our Phase Gate Process for product design and development. Involvement included all mechanical engineering and project management. Solid started by working with Magstar Technologies to summarise the product requirements and then developed multiple conceptual approaches to meet these requirements. Once the conceptual approach was refined and approved by our Client, Solid completed the detailed design in CAD, created engineering drawings, sourced suppliers and solicited proposals for both prototype and production quantities and for production tooling. Solid then coordinated all prototype component machining, assembly and testing of the first units of the product. Things worked smoothly and Solid worked with our Client to have production tooling created. Solid's engineers then reviewed 1st Article samples from production tooling and approved release to production.
Solution:
The 'Revolution' Product was born! This product is an oil filtering system designed for engines used in large equipment, long haul trucks and mining trucks. Oil from the engine’s oil pan is pumped into the top of the unit where a special design filter is being spun by an electric motor. The dirty oil is pushed through the filter media by the centrifugal force of the spinning filter which removes engine damaging particulates from the oil. The cleaned oil flows back into the engine. Use of this system more than doubles the useful life of the oil reducing engine wear.