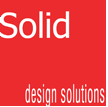
Industrial Product Development
Spotlight
Company: Thermo Fisher Scientific
Industry: Processing and Measurement Automation Equipment
HQ: Coon Rapids, MN USA
Webpage: www.thermofisher.com
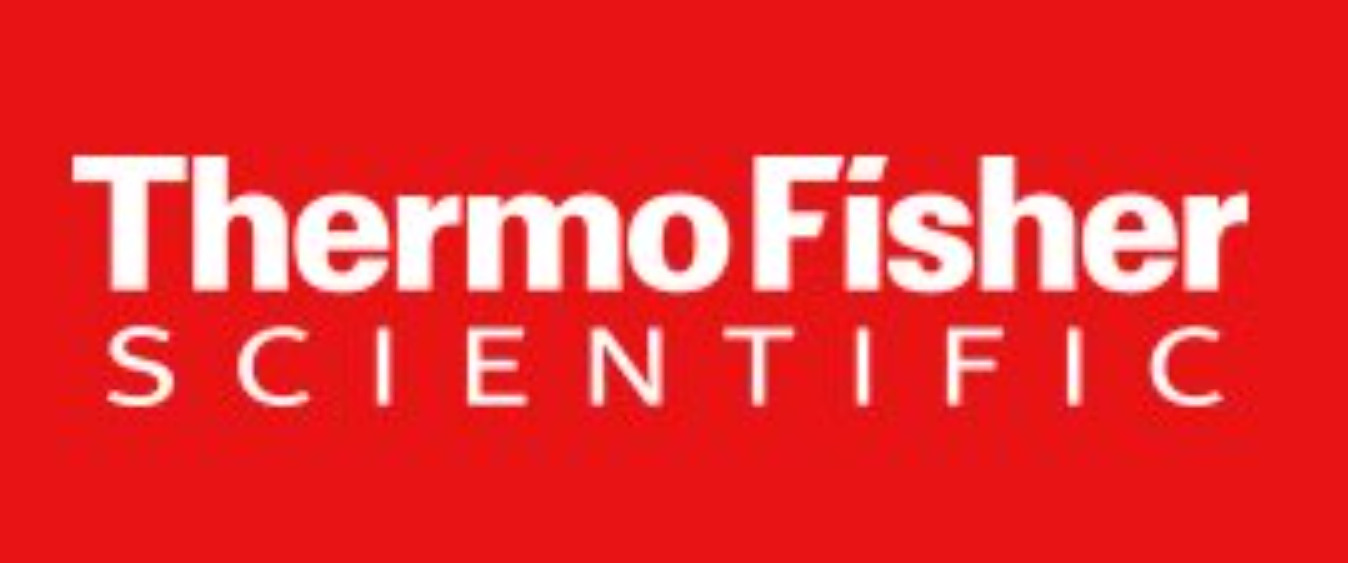
Thermo Fisher Scientific Inc. (NYSE: TMO) is the world leader in serving science, with revenues of more than $24 billion and approximately 70,000 employees globally. Their mission is to enable customers to make the world healthier, cleaner and safer. They help their customers accelerate life sciences research, solve complex analytical challenges, improve patient diagnostics, deliver medicines to market and increase laboratory productivity.

Product/Project Highlights
Metal Detection Machine
Client: Thermo Fisher Scientific
- Inspection of food products for metal fragments, fasteners, etc.
- Magnetic field disruptions are detected
- Designed for USDA 3A washdown environments with caustic cleaning agents
- Concept through detailed engineering design, assembly/testing, and making assembly fixtures
- Multiple sizes were designed to fill the product family”
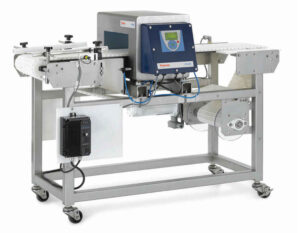
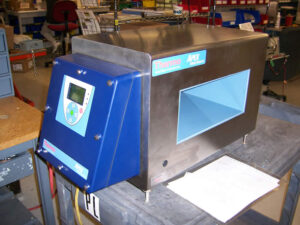
Situation:
Thermo Fisher Scientific was looking to have an updated product designed for in-line detection of ferrous metals. The product would be used mainly for inspection food products such as cake mixes, cereals, etc. and needed to meet the requirements for USDA 3A wash-down environments, using caustic cleaning agents as well as meet NEMA 4X design requirements. Solid was ready to take on the challenge.
Metal Detection Machine
Client: Thermo Fisher Scientific

Process:
Solid participated following our Phase Gate Process for product design and development. Involvement began with summarizing the product requirements, meeting with key stakeholders and moved into developing conceptual solutions for the updated product. Electrical engineering was conducted by Thermo Fisher Scientific. Together with our Client, the concept for the new machine product was refined and approved for detailed design. In the Detailed Design Phase Solid created fully defined 3D CAD models of all purchased, machined and fabricated components and built the 3D assembly in CAD software. With the Client's approval of the design, Solid created a complete sets of engineering drawings for mutiple sizes of the product, solicited quotations for prototype and production quantities and worked with our Client to set up verification and validation testing. Prototype assembly and testing was completed at Solid's facility in Mounds View, MN. After some final mechanical and firmware design tweaks, the product moved into production. Solid then design assembly fixtures to position and allign the coil with the aperature for the bonding process and to assemble the main body of the machine.
Solution:
The new metal detection product 'APEX' was ready for the market! Width: 50 to 1750 mm, Height: 50 to 900 mm. Disruptions in the magnetic field created by coil around the outside of the aperature, are detected when a metal object passes through the aperture. Multiple sizes where designed and fully documented with fully sets of engineering drawings. Participation by Solid continued through setting up manufacturing procedures, designing and making assembly fixtures and training assembly personnel at a Thermo Fisher Scientific facility in China.