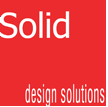
Industrial Product Development
Spotlight
Company: Multiple
Industry: Many Industries
HQ: Across the USA
Webpage:
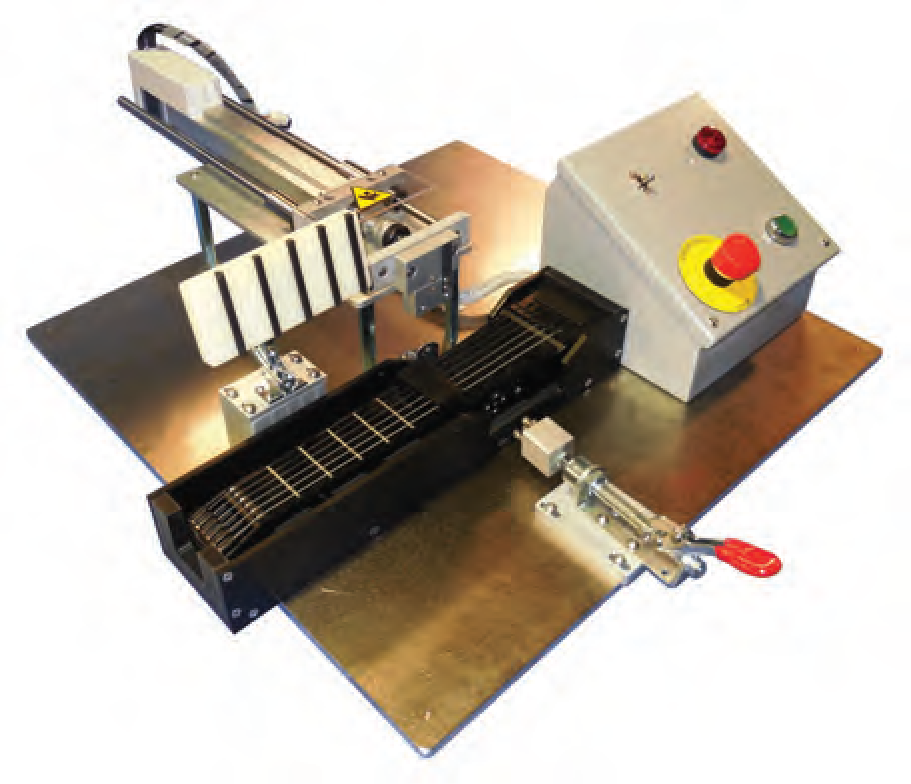
Solid has developed a wide range of fixtures and test/measurement systems. These ranged from simple work holding fixtures to complicated motion cycle tester and electronic systems test equipment.
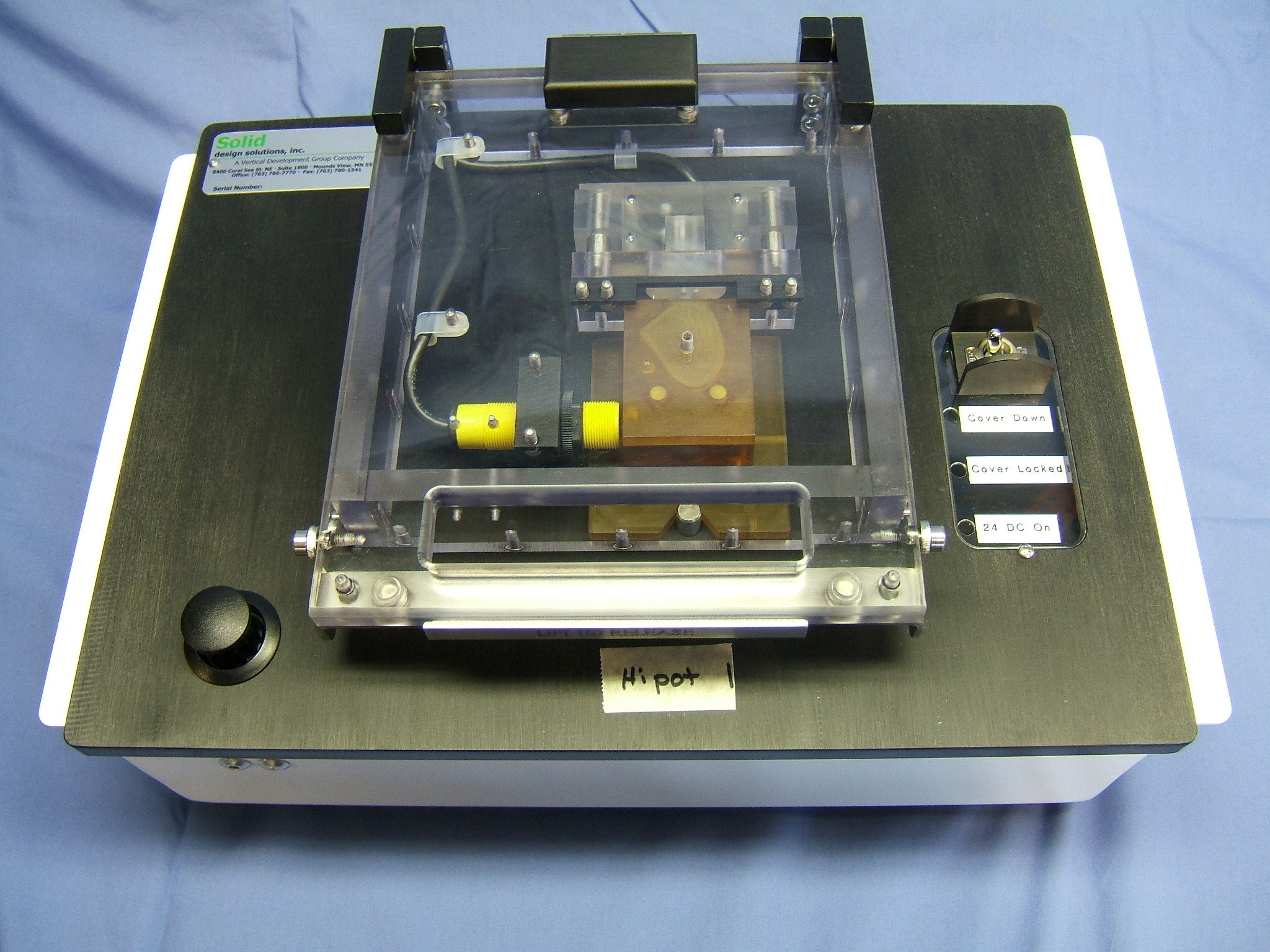
Product/Project Highlights
Fixtures and Equipment
- Work Holding fixtures for assembly
- Mechanical measurement fixtures
- Welding Fixtures
- Semi automated assembly work stations
- Electronic test systems
- Cycle testing equipment”
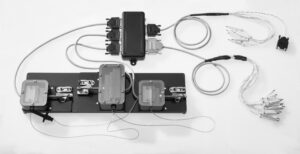
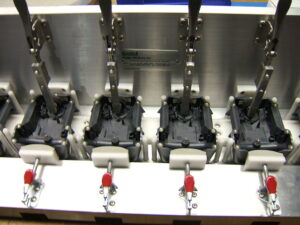
Situation:
Solid designs and develops products for consumer, industrial and medical markets. We often need to perform testing on those product designs to verify that performance meets requirements, perform life cycle testing or support production operations.
Fixtures and Equipment
Process:
At Solid we have a proven phased process consisting of the Concept Phase, The Detailed Design Phase and the Build and Test Phase. During the Concept Phase the full requirements for the equipment to be designed and built will be documented and conceptual approaches to meeting those requirements will be identified, refined and evaluated. These conceptual solution alternatives will be reviewed and discussed with our Client for their feedback. The Concept Phase ends with the selection of a concept to be developed and the estimated cost and lead time for the remaining phases will be updated based on the concept to be developed. In the Detailed Design Phase our engineers use a systems engineering approach to identify and select the required purchased sub systems and major purchased components, create detailed sketches of the system layout and begin building the 3D CAD models. As the CAD data base develops our engineers will use finite element analysis where needed to confirm the 3D CAD model designs will perform properly under the design loads these will be subjected to. The developed design will be reviewed with our Client for their input and approval, after which engineering drawings will be created for all custom components and all assemblies and sub-assemblies. A costed bill of material(BOM) is then finalized and the cost and lead-time for the Build and Test Phase is updated to complete the Detailed Design Phase. With our Client's approval we'll begin the Build and Test Phase when all the purchased subsystems, components and required services will be ordered and internally machined/fabricated components will be made. All items will be inspected against the engineering drawings or specification when completed or received. Subsystems will then be assembled and tested where appropriate before assembling the complete machine. Control system programming will then be conducted and testing will begin. Once programming has been completed and testing confirms performance of the new equipment we'll conduct a Factory Acceptance Test(FAT) with our Client to complete the Build and Test Phase. More details about our machine development process can be found on our website at SolidDesignAustralia.com.au
Solution:
Whether you're looking for simple fixtures to improve operator efficiency or you need a semi automated assembly work station for a cleanroom application Solid can get it designed and delivered for you.